Tinius Olsen - The Making of Testing History
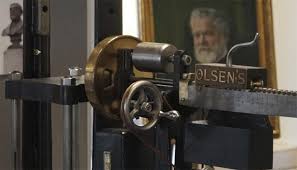
Shortly after the end of the Civil War, with industrialisation gaining momentum in the United States and new construction sprouting up everywhere, there was an increasing need for better ways to test the materials used in machinery, in buildings, and elsewhere. Engineers decried the lack of reliable information on the properties of materials; “The art of construction….is involved in mystery and obscurity,” noted Van Nostrand’s Engineering Magazine. “The knowledge of materials is at present absolutely empirical. Before the constructor makes use of either a new material, or an old one in a new form, the only safe method is to experiment.” Without some means of testing the strength of materials before their use, however, these experimental results were likely to take the form of explosions or building collapses. From the 1850’s on, various devices for testing materials had been developed, but the goal of a truly universal testing machine proved elusive until 1880, when an u