Tinius Olsen Helps Drive Automotive Sustainability Through Hydrogen Fuel Cell Technology
Tinius Olsen Helps Drive Automotive Sustainability Through Hydrogen Fuel Cell Technology
The race to meet net zero is hotting up as the development of alternatives to battery power start to come online. Tinius Olsen is currently supporting one of them alongside the UK’s leading developer of hydrogen fuel cell technology, Intelligent Energy. Prime Minister Rishi Sunak recently announced that ‘a new electric vehicle was being registered in the UK every 60 seconds’ as he outlined the government’s decision to delay the ban on the sale of new petrol and diesel vehicles until 2035. That’s just under half a million cars a year at the present rate but the question is already being asked “is electric really going to be the best option in the drive to reach net zero?”Let’s consider the pros and cons of electric, or battery powered vehicles. On the upside they’re obviously very environmentally friendly, cheaper to run than the fossil fuel variety, require less maintenance and some of them are extremely quick.
On the downside there’s limited battery range, battery lifespan issues and cost, long charging times and, ironically, environmental impact implications based on current non-sustainable electricity generation and the processes and materials involved with battery production. And they’re very expensive.
So, all things considered, if the downsides are steering you away from the electric battery option, is there any other power source you can fall back on that may not change your current fuelling activities and still help towards stemming climate change? Hydrogen fuel cells might just be the answer.
“Firstly, neither of these technologies are new,” says Oliver Jackson, Senior Research Engineer at Intelligent Energy based in Loughborough, who are the UK’s leading developer of hydrogen fuel cell technology. ‘What we recognise as the first hydrogen fuel cell was developed by Welshman William Grove in 1842, with the modern electric battery invented by Alessandro Volta some forty two years earlier. Both technologies were vying for the upper hand in terms of vehicular power-plants until the internal combustion engine proved more convenient to use and the die was cast for the next 140 years or so” continues Oliver. Fuel cells themselves work like batteries, but they do not run down or need recharging and they produce electricity and heat as long as fuel is supplied. The unit consists of two electrodes—a negative electrode (or anode) and a positive electrode (or cathode)—sandwiched around an electrolyte. A fuel, such as hydrogen, is fed to the anode and air is fed to the cathode. In a hydrogen fuel cell, a catalyst at the anode separates hydrogen molecules into protons and electrons, which take different paths to the cathode. The electrons go through an external circuit, creating a flow of electricity, whereas the protons migrate through the electrolyte to the cathode, where they unite with oxygen and the electrons to produce water and heat. “It’s an intrinsically simple system but highly efficient and of course extremely green, producing only water out of the exhaust pipe, so to speak, and doesn’t rely on electricity from the National Grid,” continues Oliver “The technology can be applied across a broad range of uses too, such as the aerospace industry, with the eventual aim of replacing fossil fuel powered jet engines with electrically powered alternatives now becoming increasingly realistic. It’s really, really exciting stuff.” Intelligent Energy emerged as a spin out from Loughborough University, where the first fuel cell project began in 1988, in 2001. Twenty two years later, following collaborations with the likes of Suzuki, Airbus, Boeing and latterly BMW, the company now employs 250 people and has offices in Japan, India and the United States.Fig 1. Shell Pipeline Inspection using hydrogen fuel cell powered UAV
“The technology has come a long way in the last 35 years or so. Our collaborations with major global companies have been a major contributor to this and these market forces are continuing to drive things forward. The need to reach net zero is obviously the main consideration, as well as reducing the cost but achieving this will need lighter, cheaper and even more efficient fuel cells to help achieve these targets - this is now our biggest challenge.” “This puts materials testing at the forefront of R&D, because if lighter or cheaper materials are found to work just as well, after a rigorous and extensive testing programme, then that saving can be built into the bottom line, creating a more cost effective, viable option. “Our own in-house research team are intensively using the Tinius Olsen equipment to test materials for mechanical properties, tensile, compressive and bending strength, stiffness etc. If we're going to get a finer material at a much lighter weight, we need to make sure it's strong and durable enough for its intended purpose.” “The testing lab is also used to test other areas such as electrical resistance and testing of coatings. Another key area is the transport properties of materials such as the carbon papers we use for our gas diffusion. “For all these things we need to be applying different forces to see how these properties change at different pressures, and so on.” “There are also things like gaskets and seals, we do quite a lot of testing on those, as well as supporting other departments across the business such as the mechanical design team, where they need to test new designs and prototypes. Material properties data is used by our modelling teams and quality and production teams for things like testing batch variability of products and defect analysis.”Fig 2. Intelligent Energy
“All in all, the Tinius Olsen equipment and support we receive is fundamental to what we do, so you could say they’re very much on the front line of these developments, generating confidence in materials used and the finished product” “Customers can only be as confident in your products as you are, so the more testing you undertake the more you trust your work and the more willing you are to supply customers and not have to worry. If the product isn’t to specification then it’s obviously going to be sent back, resulting in increased support in getting it to work as expected. So we need to get it right the first time and continually improve it so that the customer’s performance continues to get better. Intelligent Energy has not been distracted by changes to net zero deadlines and is continuing its development of hydrogen fuel cell technology at a rapid pace. With major automotive manufacturers such as BMW and Toyota actively producing their own hydrogen powered cars, IE’s work could well see this technology competing with, if not replacing, the current battery powered options. It’s definitely full steam ahead, Rishi Sunak’s 2035 announcement or not……………. Useful links Tensile Test Compressive Strength Test Automotive Oil & Gas Electronics ElectricalFig 3. Tinius Olsen equipment to test materials for mechanical properties, tensile, compressive and bending strength, stiffness etc.
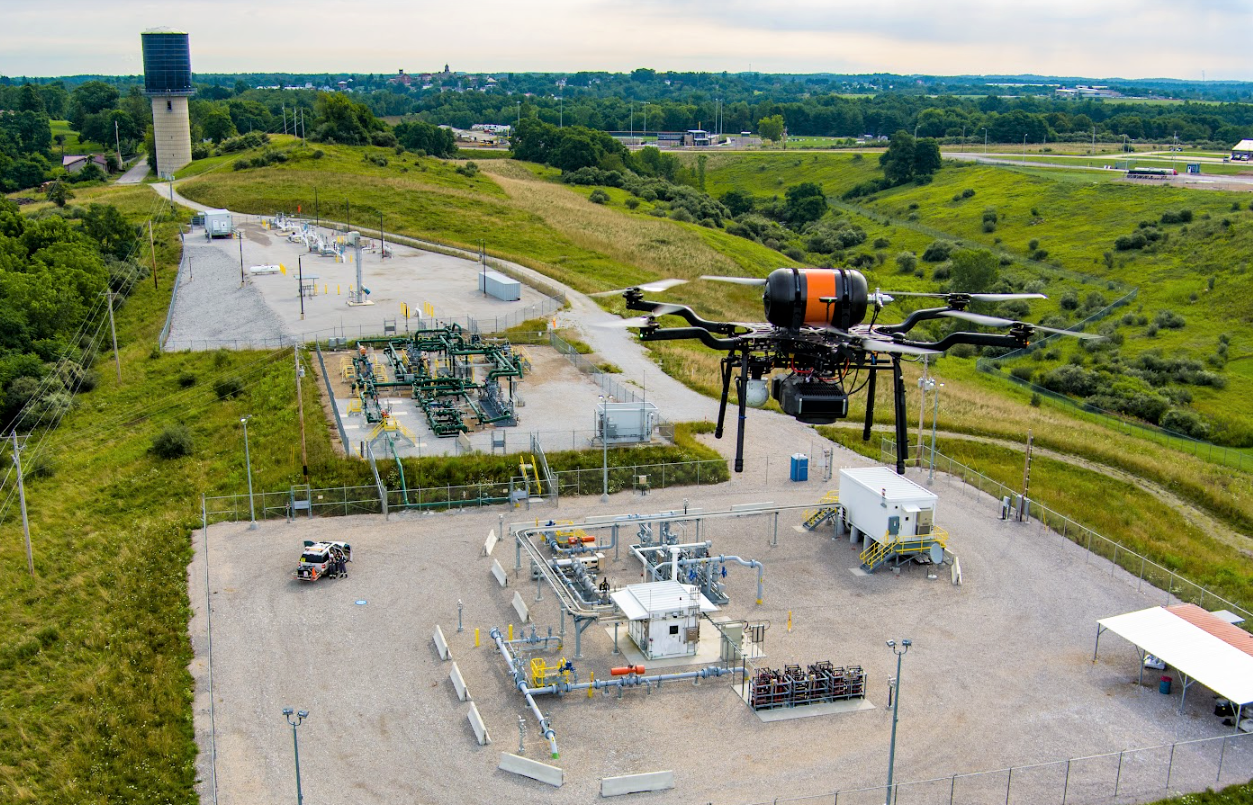
Comments