Answers from the MD........
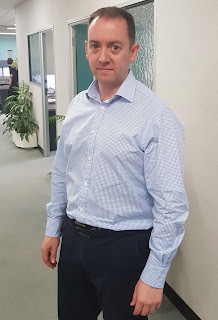
What trends/customer requirements are currently driving developments in your area of metrology?
MRP (Manufacturing Resource Planning) and nowadays, more commonly ERP (Enterprise Resource Planning) software systems are becoming the core operational and financial tools in manufacturing companies. The efficiency of a company’s manufacturing processes (product birth to death) have become progressively more transparent for financial reporting.
This detailed financial reporting provides not only a comparison of the actual production costs versus the planned or standard costs, but also reports on R&D project cycles, production re-work and delays, as well as product failures and the dreaded customer returns.
Many companies invest heavily in optimisation projects to maximise profits by trimming any excess time and material and ultimately streamlining their products and components for cost. Many of these optimisation processes are started at the design stage of a product’s lifecycle. Using automated design optimization tools such as ‘generative design’ manufacturers look at additive and subtractive processes as a combined manufacturing option, whereas previously each would have been considered separately.
These design and production engineering tools allow finance departments to produce reports quickly and provide detailed feedback. However, as with all feedback, the data must be proven before they become truly valuable to an organisation’s optimisation process.
A testing machine from Tinius Olsen provides accurate, traceable data from real world conditions, not theoretical calculations. This data is being used by more and more companies to assist with their optimisation processes. Not only in R&D and development, but all the way through to the production stages of their manufacturing process. As with ERP systems and the benefits of ‘quick data’ and snapshot reports, the Tinius Olsen Horizon software can feed this real-world data back into a customer’s database to provide a process more akin to a closed loop control system.

In addition, a variety of signal conditioners and input sources can now be directly integrated to a Tinius Olsen testing machine. These are being used by many of our customers to bring data sets together, allowing their test systems to be more flexible and meet specific requirements. These include multiple additional load cells (force sensors), direct on-sample strain inputs (strain gauges), displacement transducers, conductivity sensors, voltage signal data inputs, barcodes for batch and serialisation input, direct measurement of various sample data as well as other more specific external customer inputs.
Is there a key solution or technology that you’re excited about?
Solutions are very much customer specific, and this is something that Tinius Olsen prides itself in providing. The UTM (Universal Testing Machine) is by definition ‘universal’, but with bespoke or conventional fixtures and fittings, can quickly become a specialist testing tool for a customer’s application. The ST and SL series of testing machines are designed with a new controller, featuring a high sampling rate and allowance of additional data inputs. By adding technology ourselves or from our partners, Tinius Olsen can quickly adapt a conventional universal testing machine into a bespoke machine for a specific customer requirement.
Can you give us a specific example of how a particular solution is helping a customer?
Usually, cutting edge projects involve the signing of an NDA (non disclosure agreement) so details cannot be publicised. Solutions for clients range from fully automated testing systems down to smaller applications for customers with their own bespoke criteria. Recently we have supplied a universal testing machine to a company who are not using the machine as a tensile/compression testing machine, but instead as precision press tool. For this application Tinius Olsen was asked to design and manufacture a special press tool fixture with three independent load cells (force transducers) integrated within the fixture itself. The customer also required the machine to be finished in their own brand colours, providing a truly bespoke solution. The force signals from the three independent load cells were integrated directly into the testing machine with each sensor having its own independent signal conditioner. Within the software, each test curve of the force versus displacement data was tracked and recorded and any high points or peaks considered within the integrated pass and fail criteria. The customer is using the machine not only as a precision press, but also as its provider of batch test data, recording the results as part of their quality evidence.
What interesting developments can we expect in metrology in the coming years?
Developments in testing machine software, accessories such as extensometry and robots or co-bots (collaborative robots) will increase in the future.

In the field of extensometry, non-contact extensometers are becoming more widely used and the newer technology is becoming ever more accurate, even at very low strain percentages. This is an area of continuing development and in the coming years the market will grow as the features available increase and the price reduces.
A major trend is the growth in robotic applications and specifically collaborative robots, where a machine and cobot work together in a test department. Robotic applications were once only considered for high throughput volume testing, but now the market is also opening to lower volume batch production testing. This can be as straightforward as using a robot or cobot to integrate one or more testing machines to create a full feature testing cell.
For further information contact Richard Coombs at richard.coombs@tiniusolsen.co.uk
Comments